Le modèle GPS apporte une plus grande rigueur dans la construction des éléments géométriques permettant de définir une forme, une situation ou une position particulière de surfaces imaginées comme non parfaites (par le concepteur) ou réelle et donc non parfaites (pour le contrôleur). L'exemple ci-dessous présente le cas simple de l'épaisseur d'une pièce prismatique. Le modèle de spécification GPS | | 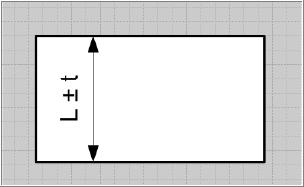 | | Le concepteur peut se contenter d'indiquer une dimension L et un intervalle de tolérance t. Pour lui, cela signifie que la grandeur de cette cote doit être vérifiée pour chaque couples de points appartenant aux deux faces opposées... et il considère, dans ce cas, que les deux surfaces sont "parfaites" | | 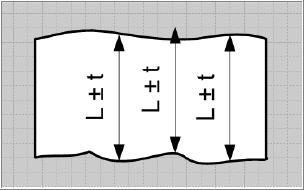 | | En réalité, les deux surfaces opposées ne sont pas parfaites et présentent des défauts. Ces défauts font qu'il peut exister des couples de points en opposition dont la grandeur qui les sépare n'est pas dans la limite de tolérance définie. Pour le concepteur, cette représentation imaginée des défauts est appelée "skin model" (modèle de la peau en anglais) | | 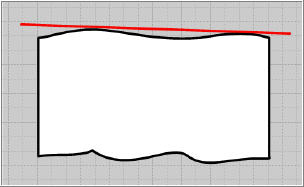 | | La particularité du modèle GPS est de proposer des règles pour définir et associer un élément parfait (le plan rouge dans l'illustration ci-contre) à une face non parfaite. La norme ISO définit donc les éléments géométriques qui interviennent dans cette étape ainsi que des opérations permettant d'associer éléments réel non parfaits et éléments parfaits. | | 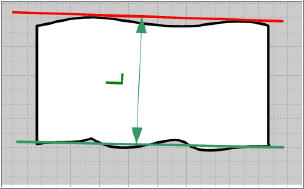 | | Le fait de définir un élément parfait permet de construire un autre élément parfait, par exemple parallèle pour l'exemple ci-contre, situé de façon théorique à une distance théorique exacte L du plan rouge, qui sert alors de référence. Cet élément particulier est appelé élément de situation car il va servir à positionner de manière précise une zone de tolérance. | | 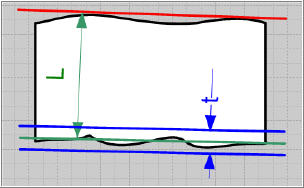 | | Dans l'exemple ci-contre, la zone de tolérance est composée de deux plans parallèles entre eux, distants d'une dimension t et équidistants de l'élèment de situation (schématisée en bleu). Pour le concepteur, la pièce sera considérée comme bonne si la face réelle non parfaite est entièrement contenue dans la zone de tolérance. | | | | | Le modèle de contrôle GPS | | La particularité du concept GPS est de proposer un modèle géométrique commun au concepteur (lorsqu'il spécifie) et au contrôleur (qui mesure). La différence entre le modèle de spécification et le modèle de contrôle tient essentiellement dans le fait que le contrôleur doit partir de la pièce réelle (non parfaite) pour extraire et associer les élèments goémtriques parfaits participants à une spécification. Pour réaliser sa mesure d'épaisseur, le contrôleur peut utiliser une machine à mesurer tri-dimensionnelle qui permet de "palper" des points réels de certaines surfaces et d'enregistrer très précisément leurs positions Les deux schémas ci-dessous montrent le principe du palpage de chaque face du prisme. | | 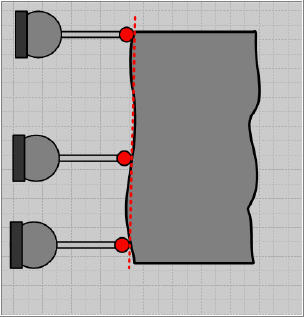 | | 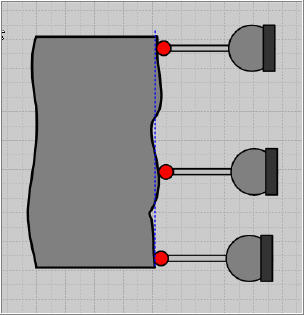 | | La détermination de points réels de la première face permet à la machine de définir un plan parfait en utilisant des algorithmes correspondants aux règles du concept GPS. | | Le palpage de la face opposée permet de déterminer la position de points réels formant une image de cette surface non parfaite. | | 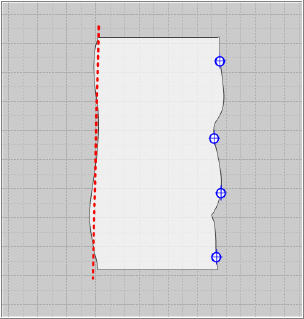 | | Une fois ces éléments déterminés, il est possible de construire un programme de vérification à l'aide d'un logiciel spécialisé. La plan de référence (en rouge sur le schéma ci-contre) devient l'image de la face réelle de référence. Les points (en bleu) deviennent l'image de la surface spécifiée qui doit vérifier une contrainte géométrique donnée. | | 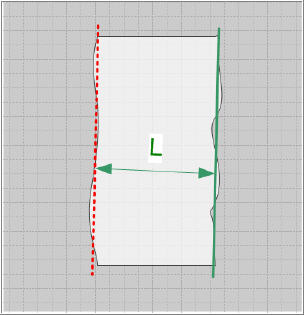 | | Le fait de définir un élément parfait permet de construire un autre élément parfait, par exemple parrallèle pour l'exemple ci-contre, situé de façon théorique à une distance précise L du plan rouge, qui sert alors de référence. Cet élément particulier est appelé élément de situation car il va servir à positionner de manière précise une zone de tolérance. | | 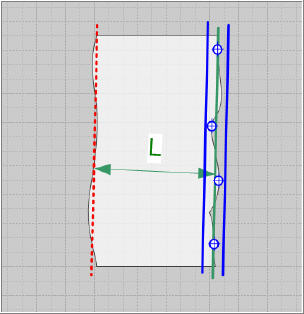 | | Dans l'exemple ci-contre, la zone de tolérance est composée de deux plans parallèles entre eux, distants d'une dimension t et équidistants de l'élèment de situation (schématisée en bleu). Pour le contrôleur, la pièce sera considérée comme bonne si les points palpés de la face réelle non parfaite sont entièrement contenus dans la zone de tolérance. |
|